“十年一实验”是什么体验?
作者 | 张双虎
“胖五”发力,“天问”腾空。火星探测让我们翘首以待。
鲜为人知的是,有一群人,为“胖五”部件加工进行了20多年研究。
在国家自然科学基金创新研究群体项目“精密制造理论与技术基础研究”(以下简称创新群体项目)支持下,来自大连理工大学的科研团队面向航空航天、信息电子、能源交通等领域对高性能装备的重大需求,系统研究了高性能复杂曲面零件精密制造、超高精度表面零件和复合材料构件精密加工、功能性表面层和多尺度微纳结构制造等理论与技术,解决了一批高端装备研制和高性能精密制造难题,成为精密制造领域国际一流的“创新军团”。
郭东明院士(中)与团队成员共同研究高性能零件加工工艺 课题组供图
航天用户高度认可
“我们特别自豪。到火箭发动机制造厂,看到车间的高端装备一大片是我们做的。”该创新群体项目负责人、中国工程院院士郭东明的话语中难掩兴奋。
运载火箭发动机喷管、燃料箱共底构件的加工制造需满足导热、高强、密封等多项高性能要求,若按照原始设计进行常规数控加工,难以满足加工要求,成为制约我国运载火箭制造的核心难题之一。
“以前,此类零件的加工,火箭制造厂往往采用手工修配、反复试凑的方式,或要加工出多件来选出一个合格件,这导致火箭关键件制造周期长、成品率低,实际应用中可靠性也无法很好地保障。”
团队成员之一、大连理工大学副教授刘海波说,“随着我国高密度发射和新航天任务的规划,这类需求非常迫切。”
上世纪90年代,郭东明意识到,装备制造已经从以往的以几何精度要求为主,跃升为以性能要求为主和性能与几何、材料并重的高端装备和产品制造。
此后他提出“高性能精密制造”理念,带领团队与企业联合攻关,研发出关联面形约束的复杂曲面加工等系列工艺,解决了大型薄壁复杂曲面零件精密加工难题。
“现在,我国这类发动机喷管冷却通道的加工都是采用我们研发的工艺和装备来完成。”
刘海波说,“应用我们的工艺方法,典型喷管冷却通道的加工周期可以从50多天压缩为20天,产品一次合格率达到百分之百。所以,航天企业对我们的认可度非常高。”
十年“种”一颗金刚石磨粒
超精密加工精度往往达纳米量级,用金刚石颗粒制作的砂轮进行磨削达到这样的精度,其难度可想而知。
“看清”磨削过程,搞清楚磨削过程中金刚石磨粒对工件材料的作用以及工件表面的微观变化,仅仅靠分子动力学仿真等理论分析远远不够,需要结合单颗粒金刚石的划切实验来模拟实际磨削,验证理论模型和分析结果。
“以前的划切实验中,金刚石颗粒划切速度低,与实际加工状态差别很大,不能反映实际磨削时材料去除状态。我们提出在实验砂轮上仅留单颗粒金刚石的纳米切深高速划切方法,不仅划切速度达到实际磨削速度,而且划切深度从零开始,由纳米量级逐渐增加到微米量级,获得了深度连续变化的超长划痕。在此基础上,就可以对工件表面划痕周围材料细微变化进行精确分析。”
郭东明说,“仅这一个实验,我们就前后进行了十年。”
研究人员一开始通过显微镜在金刚石砂轮上选择留下单颗金刚石磨粒,制备成划切工具(单颗粒砂轮)来实验,后来又发现每颗金刚石磨粒的形状、表面形态都是随机的,这意味着该实验不可重复。
“于是,我们就想设计一种具有特定几何参数的单颗粒金刚石砂轮,采用一系列特殊工艺,将超硬的金刚石颗粒加工成需要的形状,再‘种’到指定位置。”
郭东明说,“这种实验和分析方法为超精密磨削机理研究提供了先进的实验手段,对后来的工作帮助很大。”
“泡”在一线开展研究
传统机械加工中,切削刀具和磨削磨粒的硬度要比工件硬,是以“以硬磨软”方式去除材料。
但这种方式会造成零件表面损伤,直接影响零件性能。
像制造集成电路的单晶硅片,不仅要求具有高精度超光滑的表面,而且要严格控制加工表面损伤。
对硬脆单晶硅材料,采用超硬金刚石砂轮磨削时,即使优化工艺参数,仍然不可避免地产生加工表面损伤。
如何获得超低损伤表面是硬脆晶体材料超精密磨削面临的难题。
“我们想,能不能用比工件软的磨粒来磨削,这样可以减小表面损伤。于是,我们引入化学作用,通过化学反应,生成比磨粒还软的反应膜,这就可以用软磨粒砂轮去除表面材料,避免磨削损伤。这就是‘以软磨硬’。”
郭东明说,“过去是纯机械作用的‘硬切’,现在用机械和化学作用相结合的‘软切’,将加工表面损伤降到最低。”
“从2002年开始,我们经过十几年研究,用‘以软磨硬’的思路开发出超精密磨削新工艺——机械化学磨削工艺,也开发出系列化软磨料砂轮。应用该工艺方法,我们实现了单晶硅片的超高精度超低损伤磨削。这种方法不但可以用于单晶硅加工,也可以用到蓝宝石、碳化硅等硬脆晶体加工上,具有很好的应用前景。”团队成员之一、大连理工大学教授康仁科说。
和其他研究机构不同,郭东明团队成员要“泡”在加工车间。
“我们团队成员的第一个问题要来自企业。”郭东明说,“很多青年教师有1/4的时间都在一线,研究生待在加工车间的时间就更多了。”
2003年,郭东明团队来到一家企业,发现该企业虽有很好的材料,但加工效果并不理想。
“对于碳纤维树脂基复合材料等高性能材料来说,如果加工工艺不好,会影响材料性能,甚至根本无法使用。”
团队学术带头人之一、中科院院士贾振元说,“复合材料加工中经常出现分层、撕裂、毛刺等损伤。一有损伤它的性能就降低,这对高端装备制造来说是致命的。所以郭老师为团队明确了这一研究方向,我们从基础研究开始,和企业一起攻关。”
经过大量实验和分析,研究人员发现力和热是造成零件加工损伤的主要原因。但加工过程中不可能不受力,也不可能没有热量产生。
“到底多大的力最好?多高的温度影响最小?怎么来控制力量和温度?这需要从基础理论上去寻找答案。”贾振元说。
在国家自然科学基金等项目的支持下,研究人员通过大量实验,发现局部受力对加工件的影响最小。
同时,加工时“反向剪切”既能大幅度减少损伤,又能将刀具寿命延长3~5倍,同时还大幅度简化了工艺。
有了深厚基础研究作后盾,该团队在精密制造理论与技术方面取得了一系列重大创新成果,多项成果用于重大型号研制与量产。
“在郭老师的带领下,我们建成了一支有影响力的队伍。我们和合作单位、相关企业关系密切,通过‘产学研用’的配合,我们的队伍也在实践磨炼中成长起来。”贾振元说。
致力“聚焦、贯通和融合”
《中国科学报》:您认为基础研究在解决应用技术难题上能起到怎样的作用?
郭东明:解决尖端技术问题不能局限于技术本身,因为突破技术瓶颈往往需要基础研究的突破作支撑。我们虽然做的是基础研究,但大部分问题来自生产实践。
要弄清需求、瞄准问题,就要求拿出一定的时间到企业去深入了解关键技术难题是什么、根源在哪儿,然后凝练出制约技术的基础理论问题,再进一步思考和研究如何取得突破。
基础研究积累不够,会导致遇到技术难题需回过头来做基础研究。基础研究和应用技术之间的关系很紧密,也特别复杂,互相影响甚至是耦合关系,这种复杂的关系单靠企业很难解决问题,往往需要多学科、多领域的人才合作,通过技术牵引下的基础理论突破来解决。
《中国科学报》:您的研究对我们成为“制造强国”或解决制造业“卡脖子”问题可起到怎样的作用?
郭东明:要成为制造强国,关键是提高我们制造的质量和水平。
工艺上的进步,很大程度上取决于与之相关的基础研究支持。
我国在高端装备方面的差距,源于我们对工艺研究和影响技术的基础理论研究不够深入、不够系统。
超高精度加工并非只是简单的精度提高,影响精度的因素非常多,它牵涉诸多方面,一定程度讲,它也是一个系统工程。
要解决“卡脖子”问题、要成为制造强国,首先要解决超高精度制造方面的难题。我国在精密和超精密制造方面目前布局还很不够,没有形成系统的力量。
我希望我们在这方面的研究能弥补一部分或解决一部分问题。
《中国科学报》:在超高精度制造方面,目前我们处于什么水平?团队下一步的发力点在哪儿?
郭东明:我们虽然实现了“单点突破”,但从总体上说,和先进国家还有差距。
我国装备制造方面的差距主要体现在制造装备的性能上。
下一步我们要在聚焦、贯通和融合上做好文章。
一是要聚焦高端,即聚焦高端装备的性能保证。
所谓高端,就是做出来的装备性能要高。
以前我们长期聚焦在提高制造精度上,产品性能和精度有关,但并非精度高,性能就一定好。
制造的理念需要从精度跃升到性能上,这也是20多年来,我们从实践和讨论中得到的启发。
二是瞄准产业,贯通研究和应用。
基础研究的内容来源于产业的技术问题凝练,以推动技术的突破为目标,只有做好基础研究,才能推动技术突破。
我们的优势是各学科人才齐备、基础研究积累厚实,应该瞄准产业需求、贯通产学研,通过这样的方式凝练问题、锻炼队伍,提升研究水平。
三是凝聚团队、融合目标。
我们围绕高性能制造这一目标,瞄准国家重大需求,通过团队文化打造团队凝聚力,将国家目标变成团队目标,将个人发展与团队目标融合,最终来解决行业或国家的高性能制造基础难题。
《中国科学报》 (2020-07-27 第4版 自然科学基金)
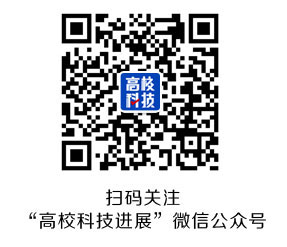
本网站转载的文章版权归原文作者所有,如有侵权请联系我们删除。

